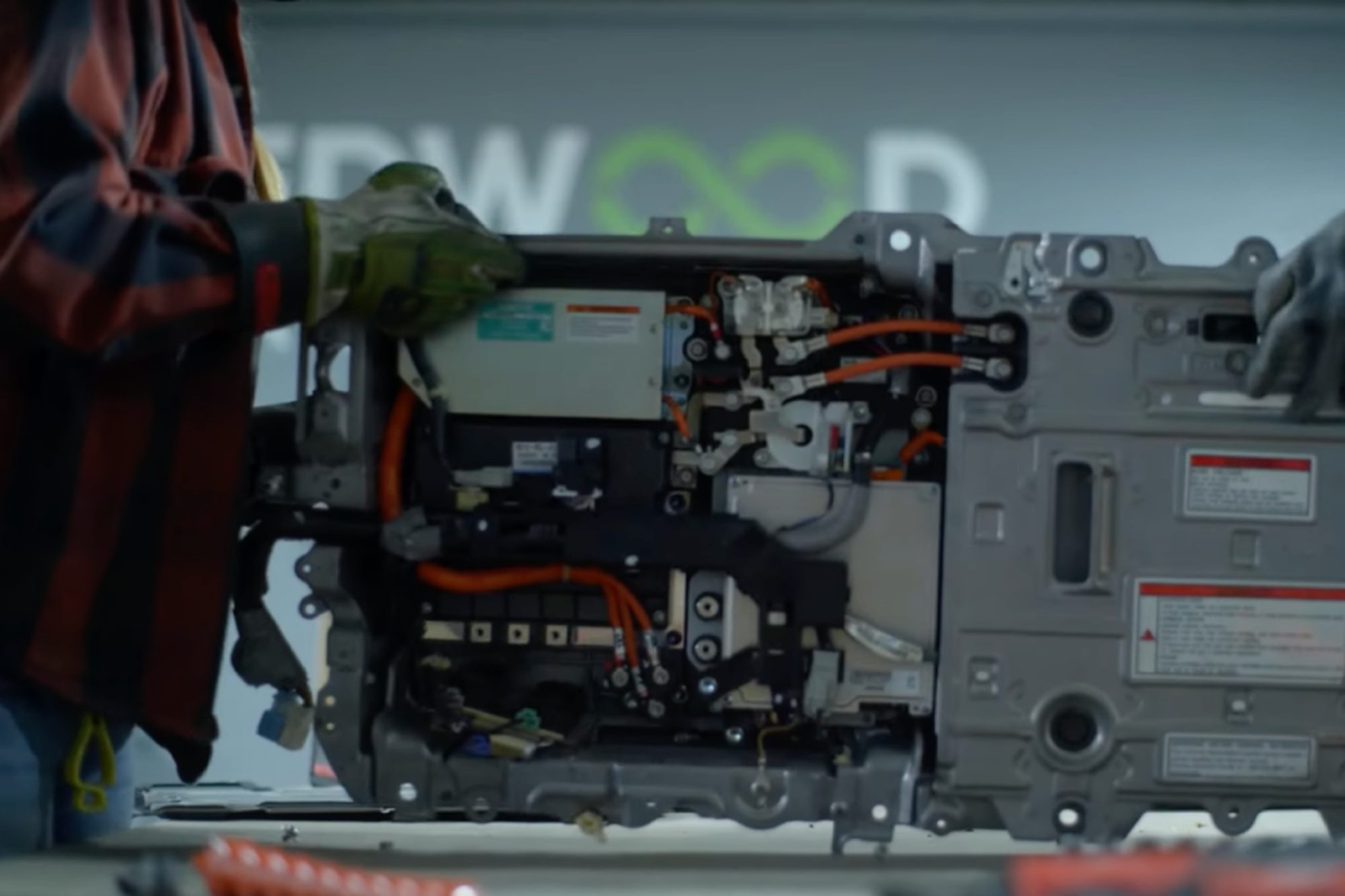
Sep 22, 2021
Redwood Materials and Ford Motor Company Announce Strategic Relationship
Read post
Last year, Redwood announced we would produce strategic battery materials in the US, supplying battery cell manufacturing partners with anode copper foil and cathode active materials. In a matter of months, our anode copper foil facility at the Tahoe-Reno Industrial Center will be complete and we will begin producing and delivering product to customers in the first half of this year.
Over the next few years, Redwood will ramp copper foil production to 100 GWh or 250,000 km of product annually; enough copper foil to build more than one million electric vehicles a year or wrap copper foil around the entire world six times!
Additionally, this site will house our hydrometallurgy recycling operations, which will allow us to feed copper from recycled lithium-ion batteries directly into copper foil production in a closed-loop. Because initially, Redwood’s production of copper foil will outweigh current supply of copper recovered from our battery recycling operations, we will also be sourcing other domestic recycled copper. Today, the US exports several hundred thousand tons of copper a year to Asia so Redwood’s utilization of this secondary supply will ensure this critical metal stays in the US.
Speaking of Asia, nearly all anode copper foil (and cathode!) production globally happens in Asia. This means that battery materials must travel tens of thousands of miles before they make their way into a final product, contributing significantly to the environmental impact and cost of battery production. By localizing copper foil in the US, we'll make this product more sustainable while driving down costs and supply chain risks. Just by localizing this product, Redwood will eliminate more than 5,500 MT of CO2 each year!
Panasonic will be the first partners who expect to source Redwood’s copper foil. Our partnership with Panasonic began in 2019 and since, we’ve been recycling all Panasonic’s manufacturing scrap from the Tesla Gigafactory. That very same material will now be recycled, and the copper contained will be remanufactured into anode foil and returned to Panasonic at the Gigafactory, just a few miles down the road. This will mark the first time batteries will be recycled, remanufactured and then returned to the same factory in a fully closed loop!
As part of our copper foil facility and expanded recycling operations, we expect to invest $1 billion in Northern Nevada over the coming years and hire more than 500 people at our Tahoe-Reno Industrial Center site. Additionally, we are still actively searching for another battery materials campus, focused on cathode production, which we plan to announce this year. At that site, we will spend upwards of $2 billion and scale cathode production to 500 GWh or five million electric vehicles by 2030. Stay tuned!