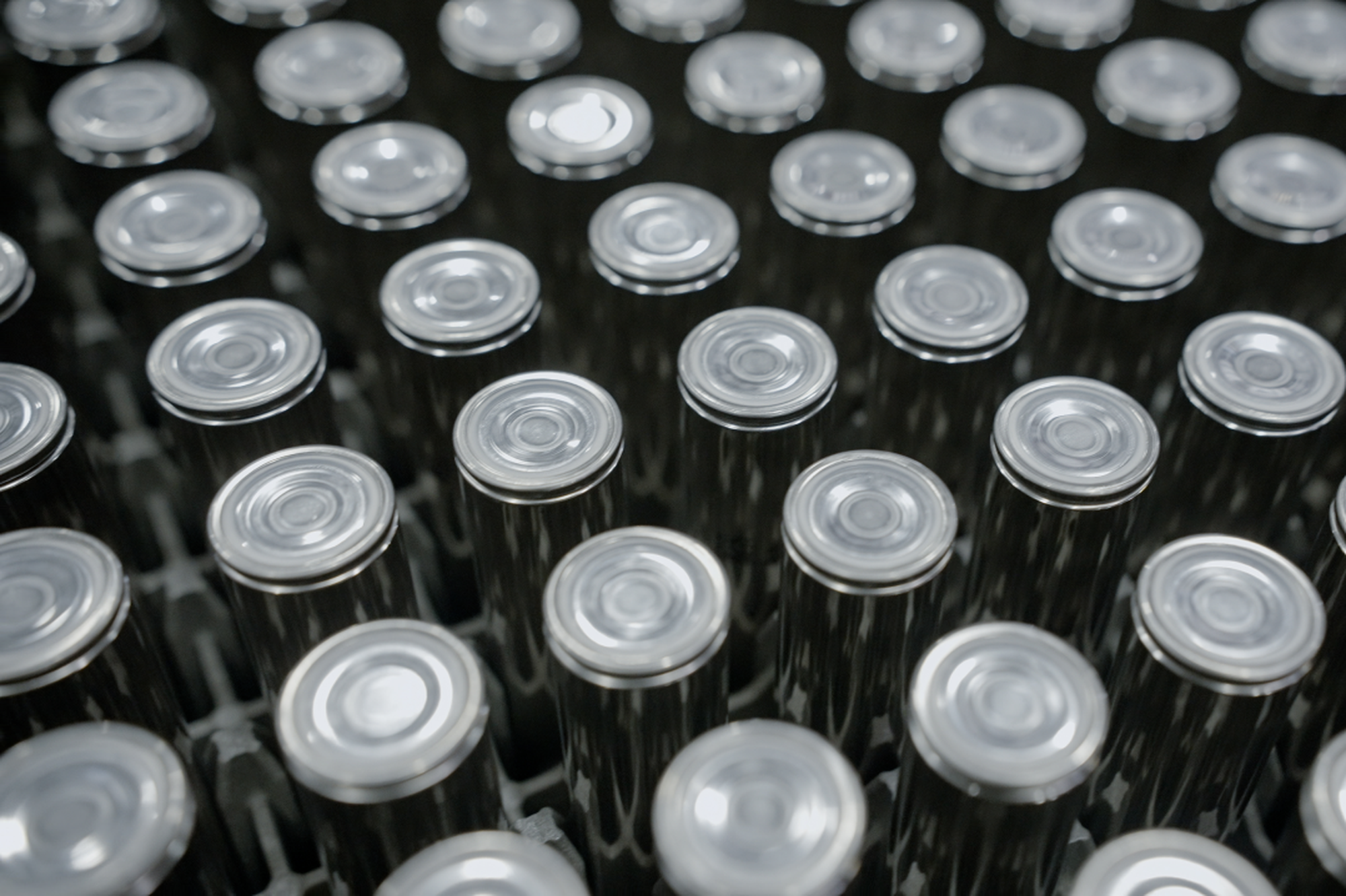
Nov 15, 2022
Panasonic to source high-nickel cathode from Redwood
Read post
At Redwood, our process involves sourcing end-of-life batteries and production scrap as well as raw materials and then recycling, refining, and remanufacturing these feedstocks into critical battery materials for North American cell manufacturers at gigafactory-scale.
Redwood is now working with Ultium Cells LLC—the joint battery cell manufacturing venture between General Motors and LG Energy Solution— to recycle production scrap from both their Warren, Ohio and Spring Hill, Tennessee facilities. Materials to be recycled include cathode and anode material as well as cell scrap.
Ultium Cells’ two facilities are each 2.8 million-square-feet operations that expect to produce more than 80 GWh combined of battery cells annually, with Redwood receiving the majority of the scrap from its manufacturing process. Ultium is already shipping material from Gigafactories in Ohio and Tennessee and the company has a third facility under construction in Michigan. With this latest collaboration, Redwood now has contracts with most of North America’s battery cell manufacturers.
Despite tremendously efficient production rates, cell manufacturing still experiences a 5-10% scrap rate on average. This equates to daily truckloads full of material, and ~10,000 tons of material annually, for Redwood to recycle and remanufacture into critical battery components for cell manufacturing.
Redwood is redefining sustainability in battery material production at our Northern Nevada campus. Compared to traditional methods of processing mined ore into battery-grade materials, our approach is significantly more sustainable. Redwood uses 80% less energy, generates 70% less CO2 emissions, and requires 80% less water, setting new standards in resource efficiency.
Our hydrometallurgy facility, the first commercial-scale nickel "mine" to open in the United States in a decade, not only recycles battery manufacturing scrap into raw nickel and cobalt but also stands as the only commercial-scale source of lithium supply to come online in the U.S. in decades. Unlike traditional mining projects that often take over a decade to become operational, we built and activated our facility in less than a quarter of the time.
According to Stanford, our process achieves at least 40% fewer emissions than other recyclers. What’s more—it’s scalable. We can process over 40,000 metric tons (about 15-20 GWh) annually and are expanding by the day.
As part of the Advanced Technology Vehicles Manufacturing Loan Program, Ultium Cells and Redwood were both selected by the Department of Energy’s (DOE) Loan Programs Office (LPO) to jumpstart critical battery materials and cell production domestically.
Our collective goals are paramount in building America’s battery supply chain and supporting a swift, sustainable transition to electric vehicles and a clean energy economy. As automakers and cell manufacturers continue to ramp up domestic battery production, Redwood stands ready to support this growth with our highly sustainable and scalable battery materials process.