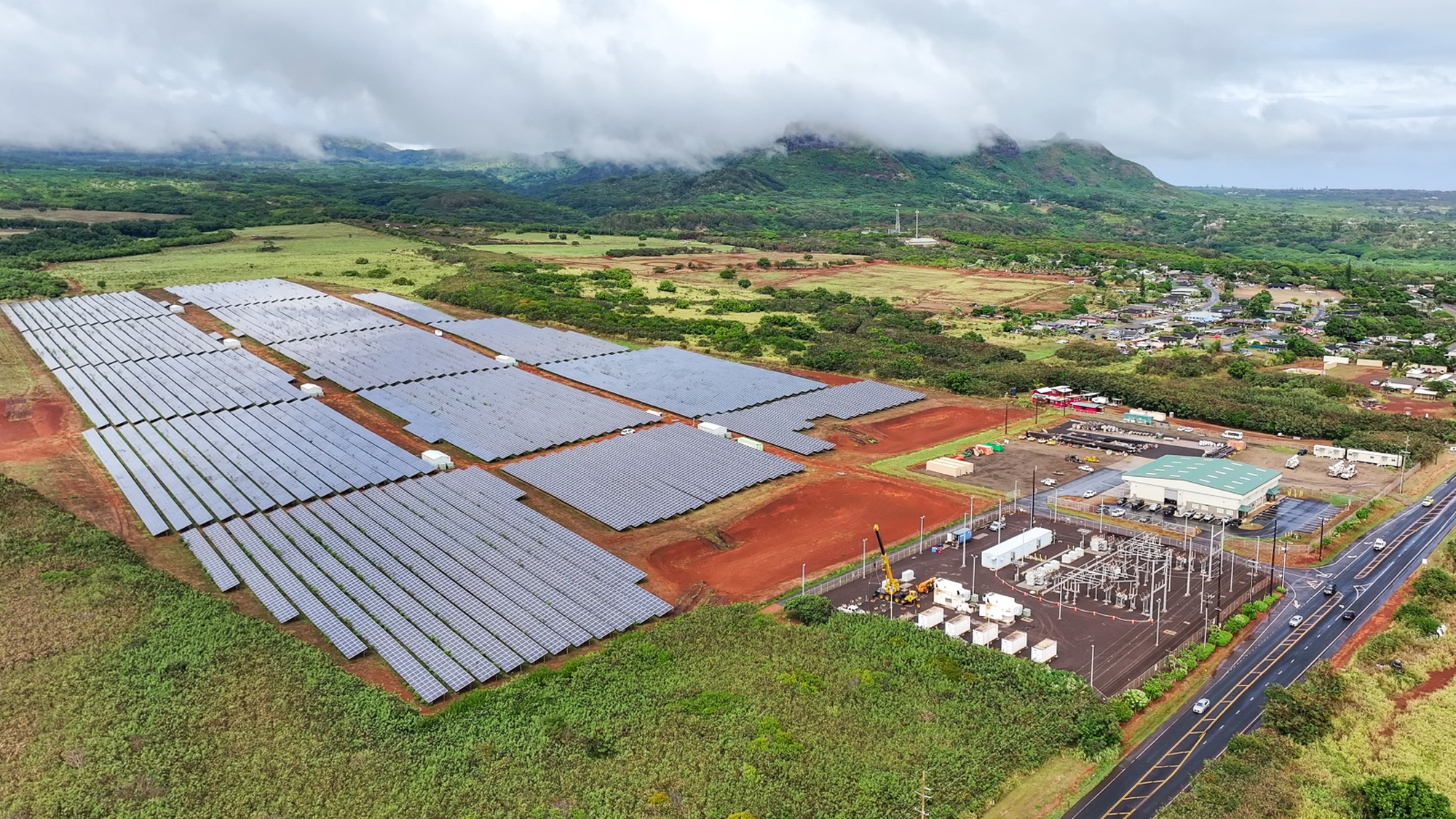
Nov 7, 2023
Decommissioning and recycling Kaua'i’s stationary energy storage systems
Read post
Operational milestones and innovations in sustainability
Over the past year at our Battery Materials Campus in Northern Nevada, we've ramped our hydrometallurgical operations, commissioned our rotary calciner for large-scale recycling, and turned on the first battery anode copper foil production in North America. These three important steps brought us closer to localizing and sustainably scaling battery materials production in the U.S. for the first time.
Our hydrometallurgy facility, the first commercial-scale nickel "mine" to open in the United States in a decade, not only recycles battery manufacturing scrap into raw nickel and cobalt but also stands as the only commercial-scale source of lithium supply to come online in the U.S. in decades. This achievement exemplifies our commitment to zero-waste and circular economy principles, showcasing our ability to produce critical battery materials locally and sustainably. Unlike traditional mining projects, which often take more than ten years to become operational, we built and activated our facility in less than a quarter of that time.
Our proprietary hydrometallurgy process significantly enhances resource recovery, successfully reclaiming 95% of lithium from scrap battery materials. The recovered nickel, lithium, and other metals are purified into intermediates or converted into chemicals for the production of high-grade cathode active materials. This process not only supports our upcoming cathode plant but also aligns with our strategic goals to minimize environmental impact and bolster domestic supply chains.
Our reductive calciner is the only calcining facility for battery recycling in North America and is crucial for processing all types of live battery feedstocks efficiently. This thermal pre-process allows us to handle live battery cells, consumer electronics, and electric vehicle modules – and can process over 40,000 metric tons (about 15-20 GWh) annually.
Redwood’s proprietary reductive calcination technology is powered by the residual energy in end-of-life batteries and uses no fossil fuels. Additionally, its reducing atmosphere minimizes carbon combustion in all forms, whether graphite, plastic, or other materials, aligning with Redwood’s commitment to achieving the lowest possible CO2 emissions while ensuring the highest level of metal recovery. Finally, reductive calcination fully liberates nickel, cobalt, graphite, and lithium from other materials, but does not create alloys or a slag waste. This not only enhances efficiency but also significantly reduces our environmental impact.
Advancing sustainable practices: Stanford’s LCA
Before we broke ground on hydrometallurgy and calcination at our Battery Materials Campus, we invited a multidisciplinary team from Stanford University to quantify the environmental footprint of our flowsheet. Stanford compared conventional refining of mined ore to Redwood’s process for recycling lithium-ion batteries and compared Redwood’s process to that of other recyclers.
According to Stanford, Redwood’s approach to recycling has a significantly smaller environmental impact than both traditional mining methods and alternative recycling technologies. What’s perhaps more important, though, is that our flowsheets are not simply an academic exercise – they’re operating today at the largest scale of any facility in North America. By utilizing our innovative combination of reductive calcination and hydrometallurgical refinement processes, all operating at low temperatures and soon powered exclusively by renewable energy sources, we achieve remarkable results. Here’s a look at the data:
Reduced environmental footprint in extraction and transport: In conventional mining cycles, extraction and transport typically account for over 30% of the environmental footprint of mined cathode materials. Our recycling process significantly reduces this impact to less than 5%, demonstrating the efficiency of our circular supply chain.
Energy and resource efficiency: Compared to traditional methods of processing mined ore into battery-grade materials, our approach is significantly more sustainable. We use 80% less energy, generate 70% less CO2 emissions, and require 80% less water, setting new standards in resource efficiency.
CO2 emissions reduction: Our processes result in CO2 emissions that are up to 92% lower than those from conventional refinement processes. This represents a substantial improvement and a significant leap towards more sustainable production methods.
Other emissions: Our unique calcining process thermally decomposes battery minerals without oxygen – meaning they are not burned, avoiding combustion emissions like NOx, CO, SO2, and PM2.5. Importantly, this method ensures that there are no liquid waste streams generated. For the small fraction of inputs that are not battery minerals, we employ a world-class emissions control system post-calcination. The emissions from this system, which are closely monitored by third parties including the Nevada Department of Environmental Protection, using the same requirements as the U.S. EPA, are publicly available.
In addition, we’re building a zero-liquid-discharge campus. Our facilities are designed to use minimal water, and we’re implementing an advanced on-site water treatment system to recycle process water back into our operations. The only wastewater discharged from our campus will be from basic amenities, such as restrooms and kitchens, ensuring that our industrial processes are completely free from liquid waste discharge.
Since the paper was written, many of our processes have evolved – some of them in response to our collaboration with Stanford – and today we achieve even lower emissions than the paper reports. For example, Stanford helped us identify that the peroxide in our hydrometallurgy process contributed significantly to our total CO2 footprint, and today we’ve redesigned our hydrometallurgy process to use no peroxide at all, an industry first.
Through this data-driven approach, Redwood is not only challenging but also changing the industry norms. Our methods underscore the potential of sustainable practices in producing battery materials and set new benchmarks for environmental responsibility in the industry.
The future of battery material production
Our recycling and refining processes are the United States' first commercial-scale facilities of their kind. In less than two years since we broke ground, our campus is already processing 30,000 tons a year of end-of-life batteries and production scrap today, and our current equipment will ramp to 60,000 tons or 15 GWh by the end of 2024. These milestones are the result of our commitment to sustainability, efficiency, and innovation. Through our ongoing efforts, we're redefining the production of battery materials, prioritizing sustainability, efficiency, and innovation at every step. Our journey continues, and we're excited to share our progress as we lead the charge towards a more sustainable future in battery material production.