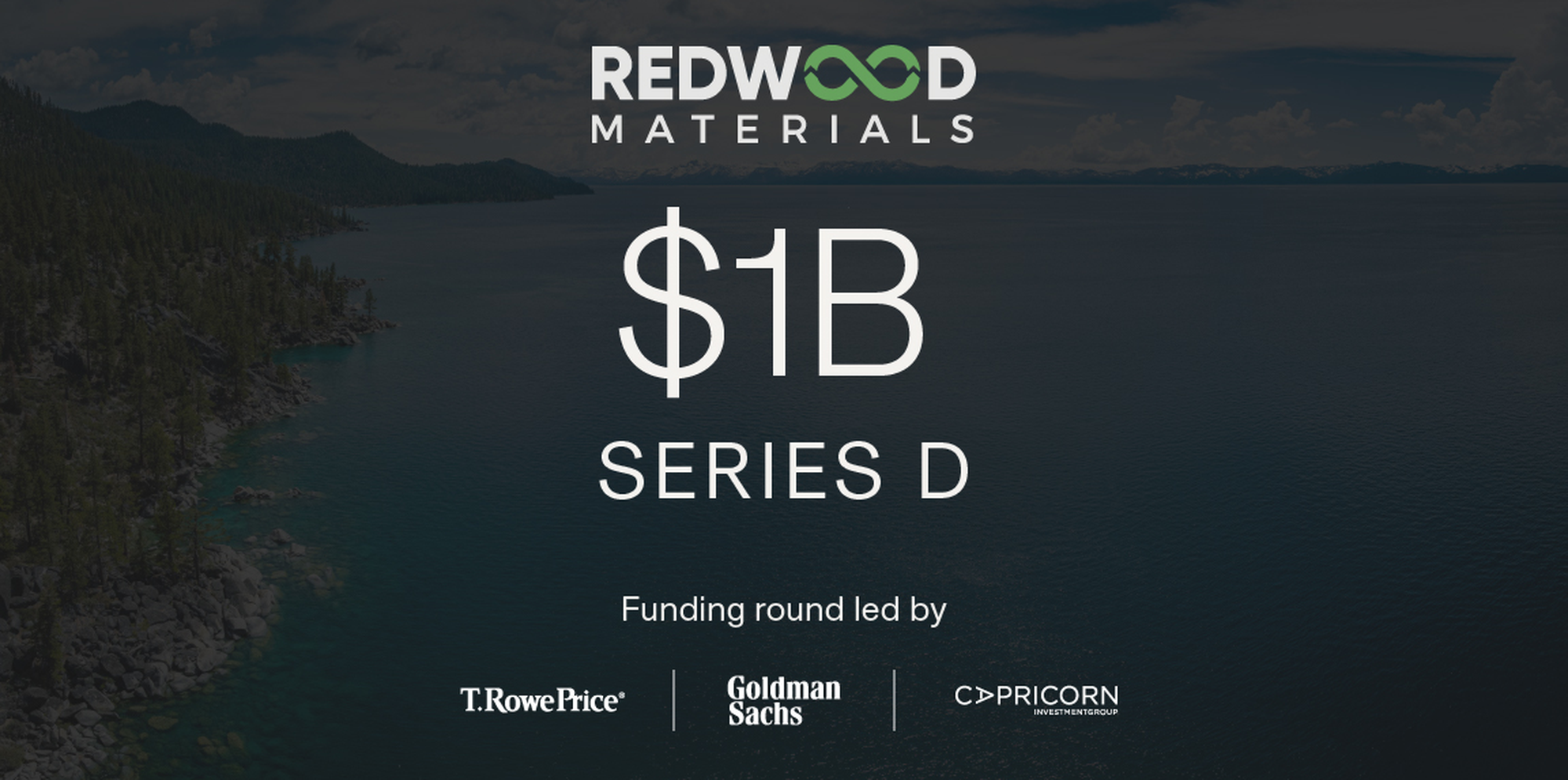
Aug 29, 2023
Redwood Materials raises over $1 billion in Series D investment round
Read post
Last year, we announced an important collaboration; Toyota and Redwood would create a closed-loop solution for batteries. Initially, our agreement focused on the collection, testing and recycling of Toyota hybrid electric vehicle batteries, all in an effort to create end-of-life pathways for those batteries. Eventually, the joint effort would expand into other areas, including battery materials supply, in North America.
Today, the second part begins to come together as we share that Toyota has agreed to source Redwood’s cathode active materials and anode copper foil as part of its production in Toyota’s upcoming North Carolina battery manufacturing plant. We believe this represents the first time that an automaker is both recycling end of life hybrid electric vehicle batteries, like those used in the Toyota Prius, and then returning those same recycled metals into that same automaker’s batteries for use in future electrified and all-electric vehicles.
Redwood is focused on creating the two most critical battery components in the US for the first time; cathode active materials and anode copper foil. Together, these two components account for the majority of the cost of a battery cell and yet are manufactured entirely overseas. Redwood’s focus and the path to decreasing electric vehicle cost, emissions, and securing our national supply chain, is to produce these components in the US, at scale, for the first time. Our mission as we build and expand the production of these battery components is to produce them from an ever-increasing amount of recycled content. Building on our work with Toyota, we will recycle their EVs and hybrid vehicles to help source metals that will build these components that will eventually end up back in their new vehicles.
For Toyota’s products, Redwood is targeting a minimum of 20% recycled nickel, 20% recycled lithium, and 50% recycled cobalt, in our cathode and 100% recycled copper in the anode copper foil, making ours the most sustainable battery materials available on earth. Our large-scale sources of domestic materials will be produced from as many recycled batteries as available but will also need to be augmented with sustainably mined material that we will source in coordination with our customers.
Today, battery components are produced via a convoluted supply chain and then imported to the U.S. only for final battery cell assembly. Redwood is making major investments in the U.S. to change this, and we’ll be spending billions of dollars to scale our technology and facilities in the next few years to bring cathode online and ramp production of critical battery components. We continue to expand our Northern Nevada facility and will soon break ground on our second Battery Materials Campus, outside Charleston, South Carolina. Both of Redwood’s campuses will recycle, refine, and manufacture battery materials, aiming to scale production of components to 100 GWh annually.
Ramping up a domestic battery materials supply chain and using the highest possible percent of local, recycled raw materials is the best way we can meet the United States’ electrification goals. We’re grateful to be working with Toyota and excited to further accelerate a sustainable transportation future through recycling and our domestic anode and cathode materials supply.