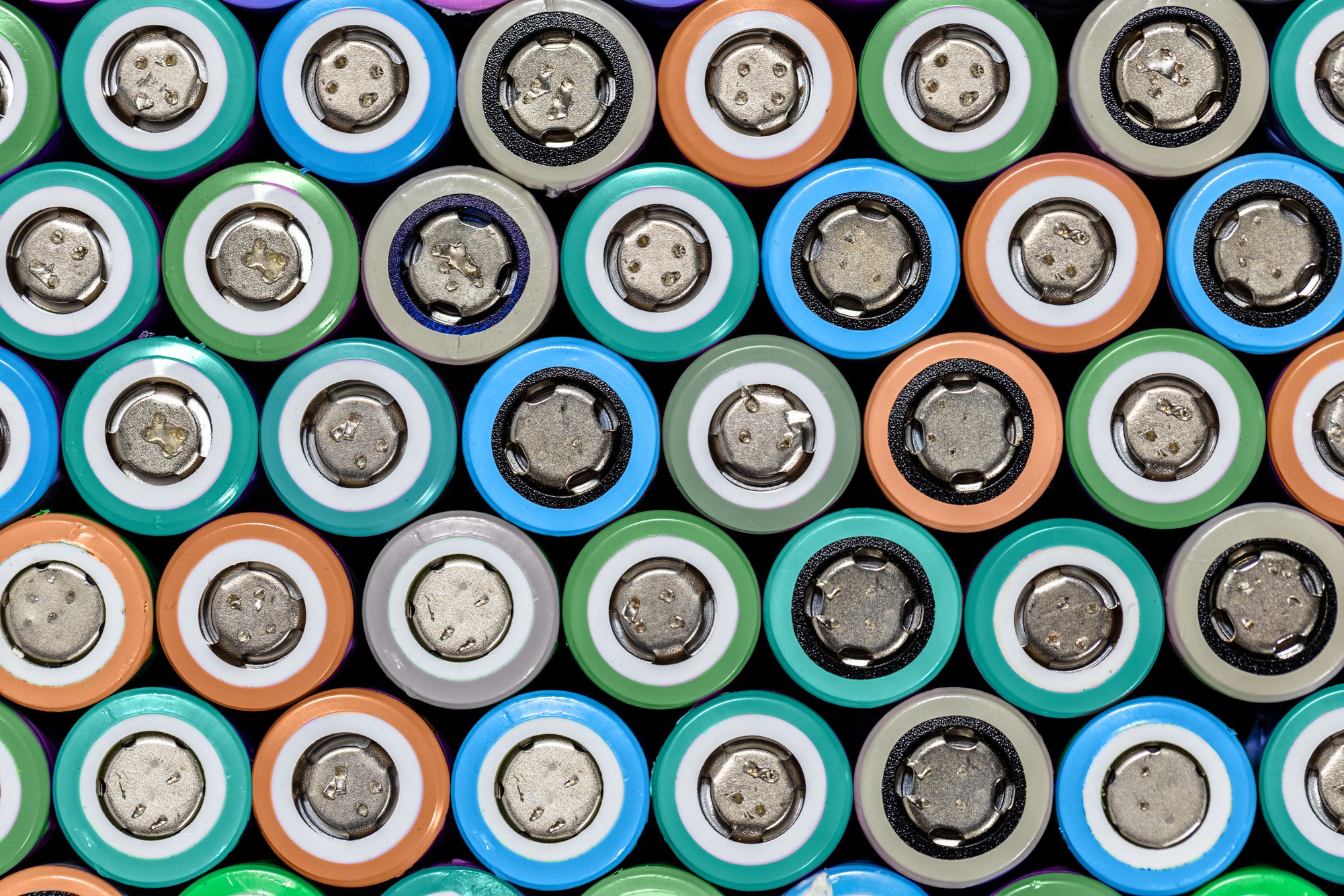
Jun 4, 2024
Lithium-ion batteries explained: Key information and uses
Read post
As the global demand for electrification of transportation and clean energy technologies grows, the need for efficient and sustainable energy storage solutions becomes increasingly crucial. Lithium-ion batteries are central to this transformation, with their performance largely determined by two essential components – the anode and the cathode.
In a lithium-ion battery, the cathode and anode are the two electrodes that enable the flow of electric charge. The cathode is the positive electrode, where reduction (gain of electrons) occurs, while the anode is the negative electrode, where oxidation (loss of electrons) takes place. During charging, electrons flow from the cathode to the anode, storing energy that can be used to power devices.
For anode, graphite is the most common material, valued for its high electrical conductivity, low cost, and stable structure. Copper foil is another example of an anode material and acts as the current collector and protective layer used in batteries.
Incorporating recycled materials into lithium-ion batteries is becoming increasingly important. At Redwood Materials, we are leading the way with our advanced recycling and production techniques. Over the past year, we have scaled our hydrometallurgical operations and commissioned a rotary calciner for large-scale recycling.
Our hydrometallurgy facility, the first commercial-scale nickel "mine" in the U.S. in a decade, not only recycles battery manufacturing scrap into raw nickel and cobalt but also provides the only commercial-scale source of lithium supply in the U.S. Our proprietary process recovers 95% of lithium from battery materials, converting recovered metals into high-grade cathode active materials.
In a recent study, the U.S. Department of Energy's Argonne National Laboratory concluded that “pristine performance can readily be obtained” from Redwood’s recycled metal-sulfates and that they will have higher capacity and lower direct current internal resistance.
Our reductive calciner processes live battery cells, consumer electronics, and electric vehicle modules efficiently, with a capacity of over 40,000 metric tons annually. The calcination process is powered by residual energy from end-of-life batteries and uses no fossil fuels, minimizing carbon combustion and environmental impact.
Using recycled materials in battery manufacturing offers several benefits:
Resource conservation: Reduces the need for mining and extraction of raw materials.
Lower carbon footprint: Requires less energy than extracting and processing raw materials.
Waste minimization: Helps minimize hazardous waste in landfills.
Cost-effectiveness: Often more economical than sourcing raw materials.
Supply chain security: Provides a reliable domestic supply of essential materials, ensuring ethical sourcing.
Lithium-ion batteries are essential for the transition to clean energy. Their high energy density and efficiency make them ideal for electric vehicles, renewable energy storage, and portable electronics. By enabling widespread adoption of electric vehicles, lithium-ion batteries help reduce greenhouse gas emissions and dependence on fossil fuels. Additionally, their use in grid storage solutions stabilizes renewable energy sources like solar and wind, ensuring a reliable and sustainable energy supply.
The anode and the cathode are fundamental to the performance and efficiency of lithium-ion batteries. Understanding the materials, manufacturing processes, and the importance of recycling is crucial for appreciating their role in the clean energy revolution. By reusing valuable materials from end-of-life batteries and manufacturing scraps, we can conserve natural resources, reduce waste, and minimize the environmental impact of mining and processing raw materials.
At Redwood Materials, our innovative approaches and commitment to sustainability highlight the potential of sustainable practices in producing battery materials and set new benchmarks for environmental responsibility. Embracing these practices in battery manufacturing can lead to a greener, more efficient energy storage industry, ultimately supporting the transition to renewable energy sources and electric transportation.