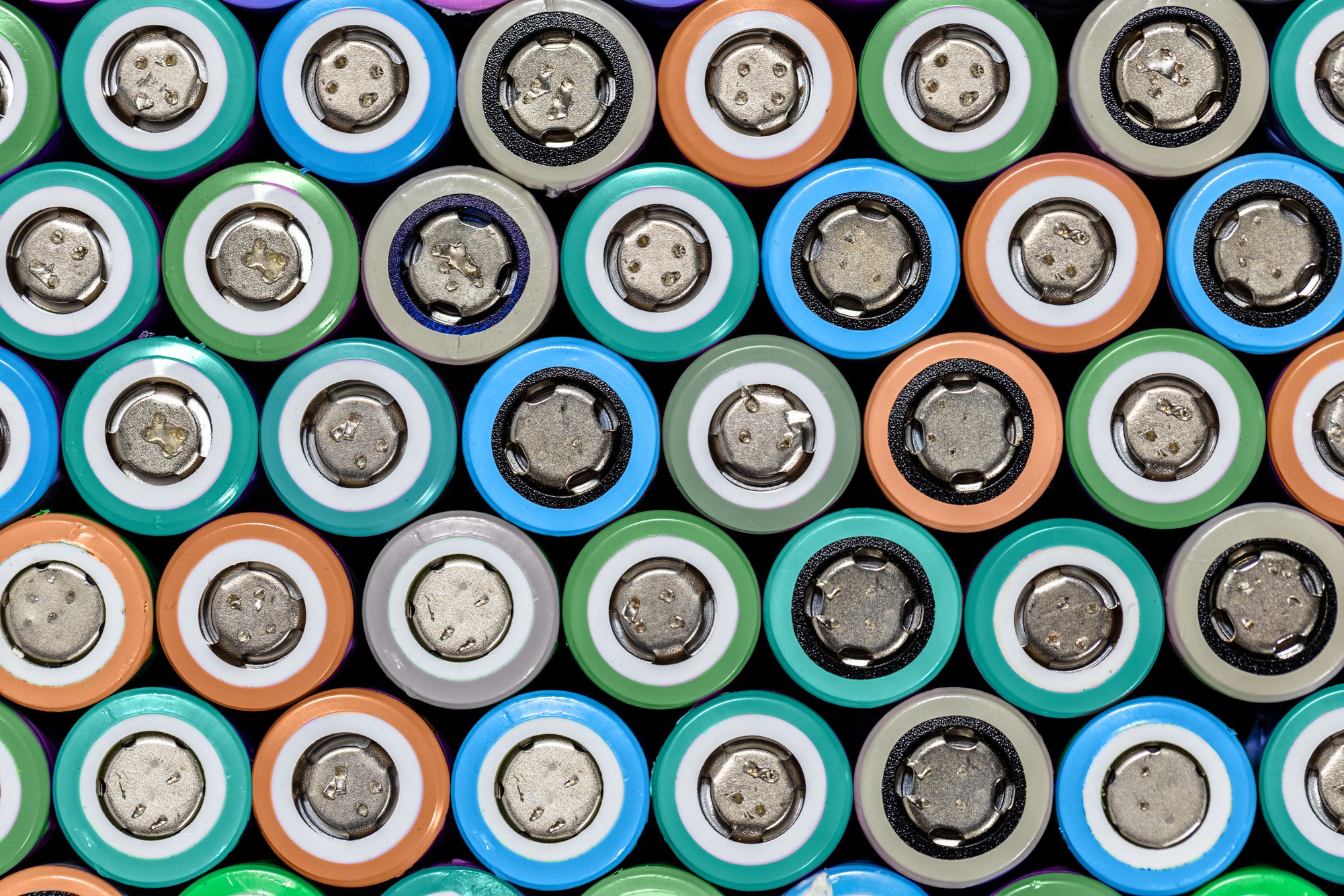
Jun 4, 2024
Lithium-ion batteries explained: Key information and uses
Read post
The battery supply chain refers to the series of processes involved in sourcing, processing, and manufacturing materials essential for battery production. This chain encompasses various stages, starting from the extraction of raw materials through refining and component manufacturing to the final assembly of battery cells for use in electronic devices, electric vehicles, and energy storage systems.
Key components of the battery material supply chain include sourcing critical minerals like lithium, cobalt, nickel, and graphite, processing these materials into battery-grade components such as cathodes, anodes, and electrolytes, and finally integrating these components into battery cells and packs. The supply chain also involves transportation, logistics, and quality control measures to ensure the efficient and reliable production of batteries for diverse applications.
The existing battery supply chain is a convoluted system that requires materials to travel tens of thousands of miles before making their way into a final product. In looking at the supply chain for a single component such as cathode, the logistics required alone contribute enormously to the overall cost and carbon footprint.
Key terms and concepts
Critical minerals: Certain minerals, termed critical minerals by the Department of Energy (DOE), are vital for battery manufacturing due to their scarcity and importance in technology. There are about 50 critical minerals, including lithium, cobalt, and nickel.
Specific metal deposits: Certain metals are only found in specific geological formations or regions due to natural geological processes. For example, lithium is primarily extracted from salt flats (brine deposits) in countries like Chile, Argentina, and Bolivia, while cobalt is often mined as a byproduct of copper or nickel mining, with significant deposits in the Democratic Republic of the Congo.
National security: Securing a stable supply of critical minerals is crucial for national security as they are essential for various industries, including defense, energy, and modern-day technology. Dependence on foreign sources for these minerals poses geopolitical risks. Diversifying sources and investing in domestic production and recycling can help mitigate these risks.
Lithium-ion batteries, ubiquitous in powering modern consumer devices and electric vehicles (EVs), rely on a blend of critical minerals like cobalt, nickel, lithium, and copper. Recycling these batteries is imperative, not only to bolster the domestic supply of battery materials but also to drive down costs for new clean energy products. Moreover, recycling mitigates the environmental footprint of batteries, crucial in a world increasingly focused on sustainable solutions. Remanufacturing battery components plays a pivotal role in this narrative, particularly in supplying US battery manufacturers. By ensuring a steady, domestic supply chain, we can meet the surging demand for EVs and consumer electronics, thus accelerating the transition away from fossil fuels and combating climate change.
Redwood Materials is at the forefront of ensuring that the United States meets its clean energy and electric vehicle ambitions. We are dedicated to developing a domestic, secure, and sustainable battery supply chain.
Recycling: We focus on collecting and recycling end-of-life lithium-ion batteries from EV battery packs to consumer devices, turning potential waste into high-value battery materials.
Refining & processing: Our facilities process and refine critical minerals contained in these batteries, ensuring their optimal reuse.
Remanufacturing: We specialize in re-manufacturing sustainable battery materials, particularly cathode active materials and anode foils, essential for domestic battery manufacturing.
By integrating recycling with refining and production, we aim to produce these components at scale, using as much recycled content as possible. We are able to recover more than 95% of the critical minerals from batteries (like nickel, cobalt, lithium, and copper) and can use those metals to remanufacture battery components (anode and cathode) that we can supply directly back to U.S. battery manufacturers.
This approach is not only more sustainable but also cost effective, challenging the traditional battery supply chain model that historically depended heavily on Asia.
This reliance poses a significant risk, potentially offshoring over $600 billion in economic value in the coming decade. Redwood is strategically countering this by investing in America – onshoring crucial elements of the battery value chain, fostering technical expertise, and generating high-quality jobs. Our efforts are giving the nation’s clean energy technology and electric vehicle adoption the strongest foundation for success.
As Redwood CEO JB Straubel notes, “Electric vehicles are an energy security product, but they’re only as secure as our ability to make them."
Listen to the video below to hear JB share more on the United States' strategic battery stockpile and the challenge and opportunity of localizing our supply chain.