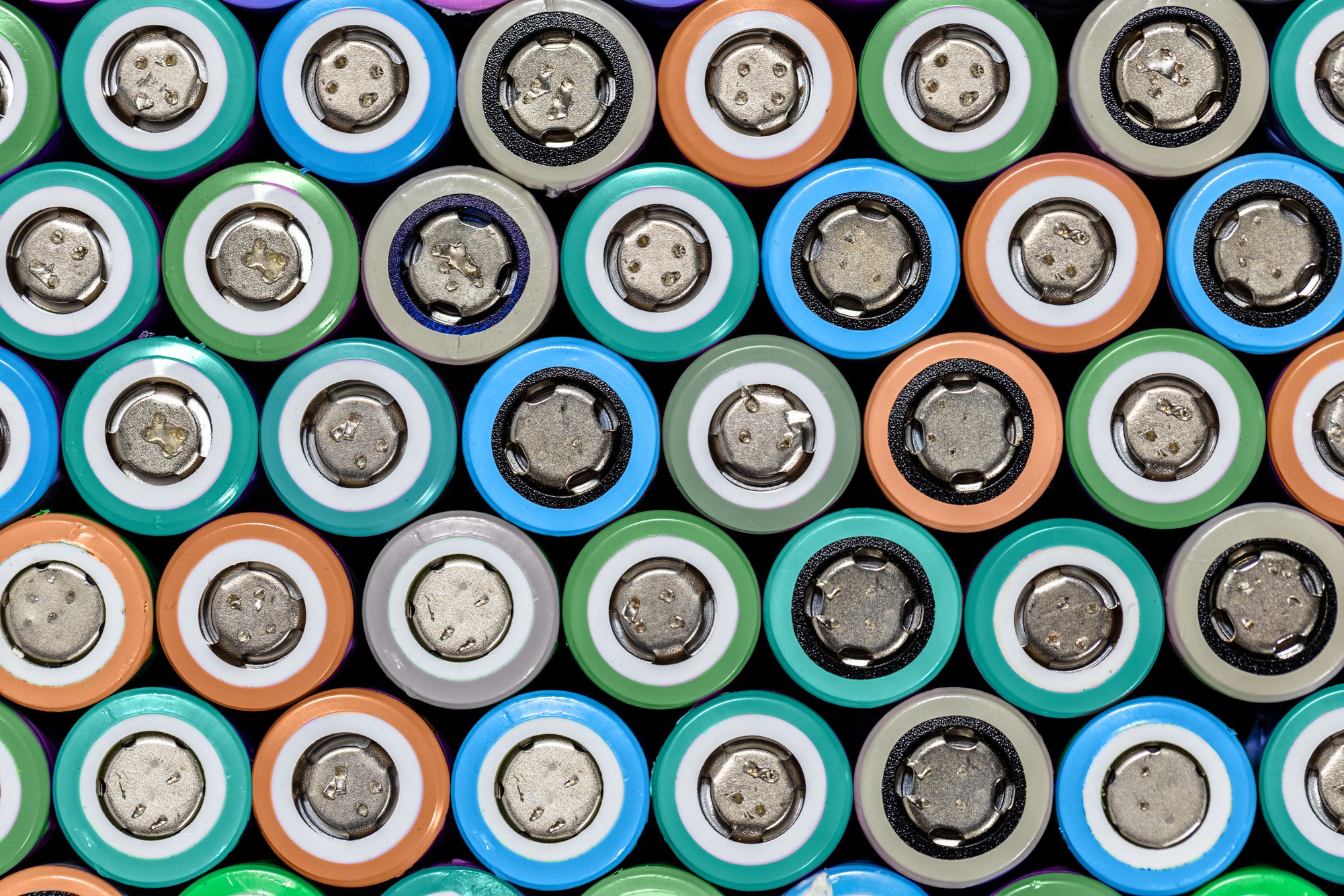
Jun 4, 2024
Lithium-ion batteries explained: Key information and uses
Read post
In the landscape of automotive technology, there are two prominent contenders: Internal Combustion Engine (ICE) cars and Electric Vehicles (EVs). ICE cars predominantly rely on fossil fuels, a finite resource with significant environmental consequences, contributing to pollution and our world’s climate crisis. In contrast, EVs harness the power of critical minerals such as lithium, cobalt, nickel, and graphite, which form the backbone of their advanced battery systems.
The demand for EVs has continued to grow, which in-turn, has increased the need for lithium-ion batteries and critical minerals. In 2024, Stanford University released a study that detailed the challenges this growing demand creates for our supply chain:
Notably, critical minerals have the remarkable ability to be recycled indefinitely, a key insight underscored by JB Straubel, Redwood’s founder & CEO during a Big Ideas Stanford University Lecture in 2024:
Redwood’s mission is to increase sustainable battery materials production and build these materials from an increasing amount of recycled content, including cathode active material, the component in a lithium-ion battery primarily responsible for determining the battery performance, safety, and cost.
In fact, Redwood’s very high recycled content makes it the most sustainable battery material available on earth. The U.S. Department of Energy’s Argonne National Laboratory tested Redwood’s recycled metal-sulfates to validate the performance of the cathode material when put into the production of battery cells and showed identical cycle-life performance and concluded “pristine performance can readily be obtained” from Redwood’s recycled metal-sulfates.
By keeping these critical materials within a closed loop ecosystem, Redwood pioneers a sustainable paradigm, where recycled minerals seamlessly integrate into new generations of batteries and cars, epitomizing the vision for a circular economy in the automotive industry.
Making more sustainable battery materials
Today, Redwood receives more than 20 GWh of lithium-ion batteries annually, which equates to more than 100,000 cars, 1.576 billion cell phones or 40,000 metric tons/year. We recover more than 95% of the critical minerals from batteries and then remanufacture those materials into battery components that we supply directly back to U.S. battery manufacturers.
To better understand our environmental footprint, we invited a multidisciplinary team from Stanford University to quantify the environmental footprint of our flowsheet at our Battery Materials Campus in Northern Nevada. Stanford compared conventional refining of mined ore to Redwood’s process for recycling lithium-ion batteries and compared Redwood’s process to that of other recyclers.
According to Stanford, Redwood’s approach to recycling has a significantly smaller environmental impact than both traditional mining methods and alternative recycling technologies. Here’s a look at the data:
Compared to traditional methods of processing mined ore into battery-grade materials, our approach is significantly more sustainable. Redwood uses 80% less energy, generates 70% less CO2 emissions, and requires 80% less water, setting new standards in resource efficiency.
Redwood is just getting started, and we'll continue to increase sustainable battery materials production and build these materials from an increasing amount of recycled content.