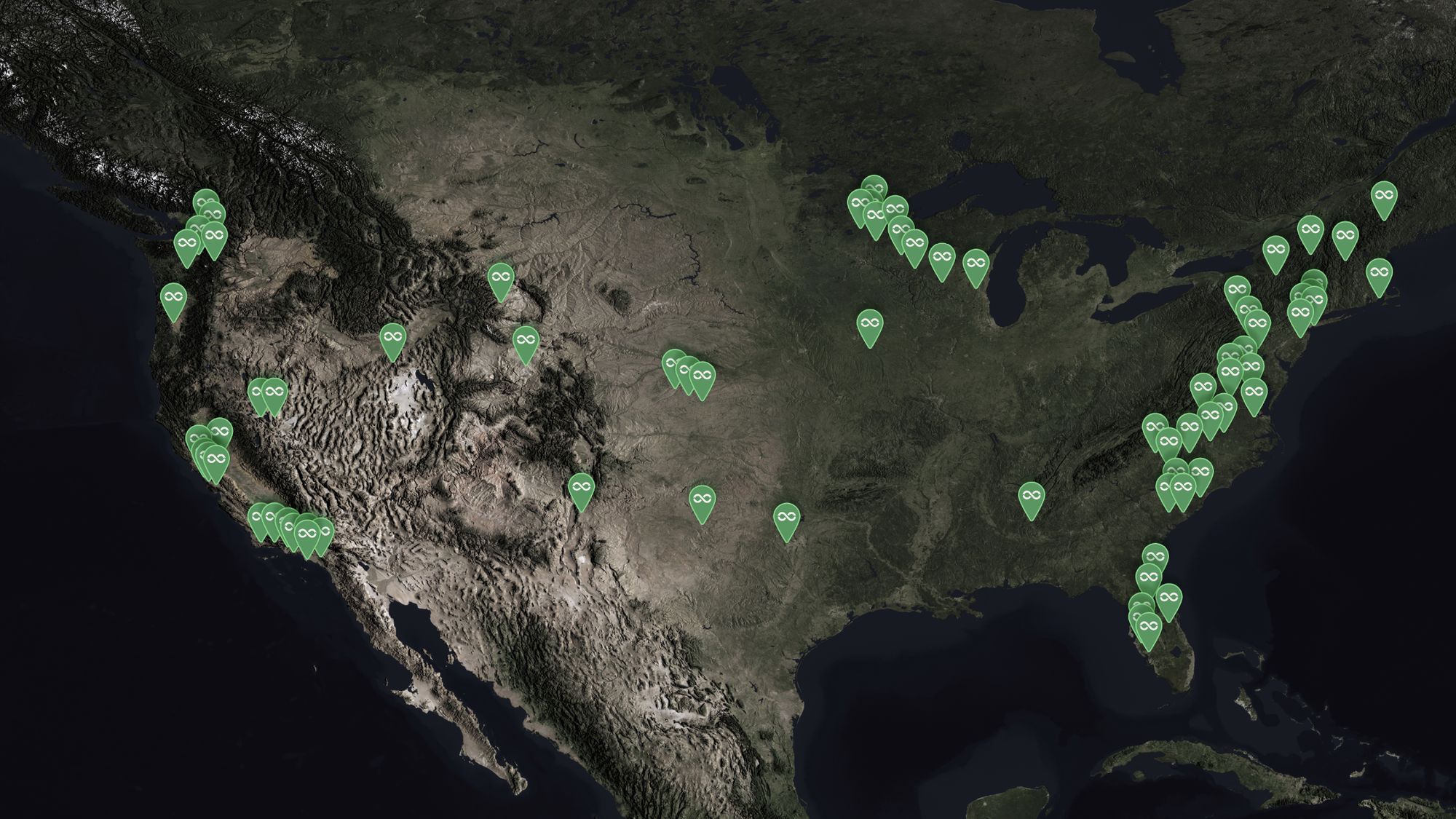
Jul 2, 2024
Where to find battery recycling near you
Read post
Batteries are comprised of multiple types of critical minerals, such as lithium, cobalt, and nickel, which are valuable resources that can be obtained in two different ways:
Virgin or terrestrial mining: The traditional method by which metals are originally extracted from the Earth is through what’s called virgin or terrestrial mining.
Recycling: The process of recovering valuable materials from used batteries, refining them, and reusing them in the production of new batteries. This ensures a circular supply chain, reducing the need for virgin materials and minimizing environmental impact.
As demand for batteries grows, so does the need for critical minerals. While mining will remain necessary in the near term, it's essential that we mine these resources responsibly. Recycling plays a key role in meeting this demand until the first generation of products reaches end of life. Looking ahead, we anticipate that recycling will largely replace terrestrial mining, driving a more sustainable and circular supply chain.
Here’s what to know about recycled battery materials compared to virgin-mined materials across performance, environmental impact, and cost.
There is often skepticism about whether recycled materials can match the performance of virgin-mined content. To address this, Redwood partnered with the U.S. Department of Energy’s Argonne National Laboratory to validate the performance of our recycled metal-sulfates in battery cell production.
The results were clear: our recycled metal-sulfates delivered identical cycle-life performance, discharge capacity and Coulombic efficiency when compared to cathode materials made from virgin-mined metals.
Argonne also concluded that “pristine performance can readily be obtained” from Redwood’s recycled metal-sulfates, noting they offer higher capacity and lower direct current internal resistance.
In addition to working with Argonne to measure performance, we also teamed up with a multidisciplinary team from Stanford University to quantify the environmental footprint of our recycling process. Stanford compared conventional refining of mined ore to Redwood’s process for recycling lithium-ion batteries and compared Redwood’s process to that of other recyclers.
Compared to traditional methods of processing mined ore into battery-grade materials, Stanford found that our approach is significantly more sustainable. We use 80% less energy, generate 70% less CO2 emissions, and require 80% less water, setting new standards in resource efficiency.
In addition to the performance and sustainability benefits, the economics are compelling for recycled content. At Redwood, we’re already producing material at a cost that’s competitive with virgin-mined metal, and as we continue to scale, this will become even more apparent.
While there will be a need for virgin-mined metals for decades to come, recycled materials offer an attractive alternative to fill the supply gaps for critical minerals we’ll face over the coming years, and these benefits will only continue to increase.